9 Important Differences Between Qualification and Validation
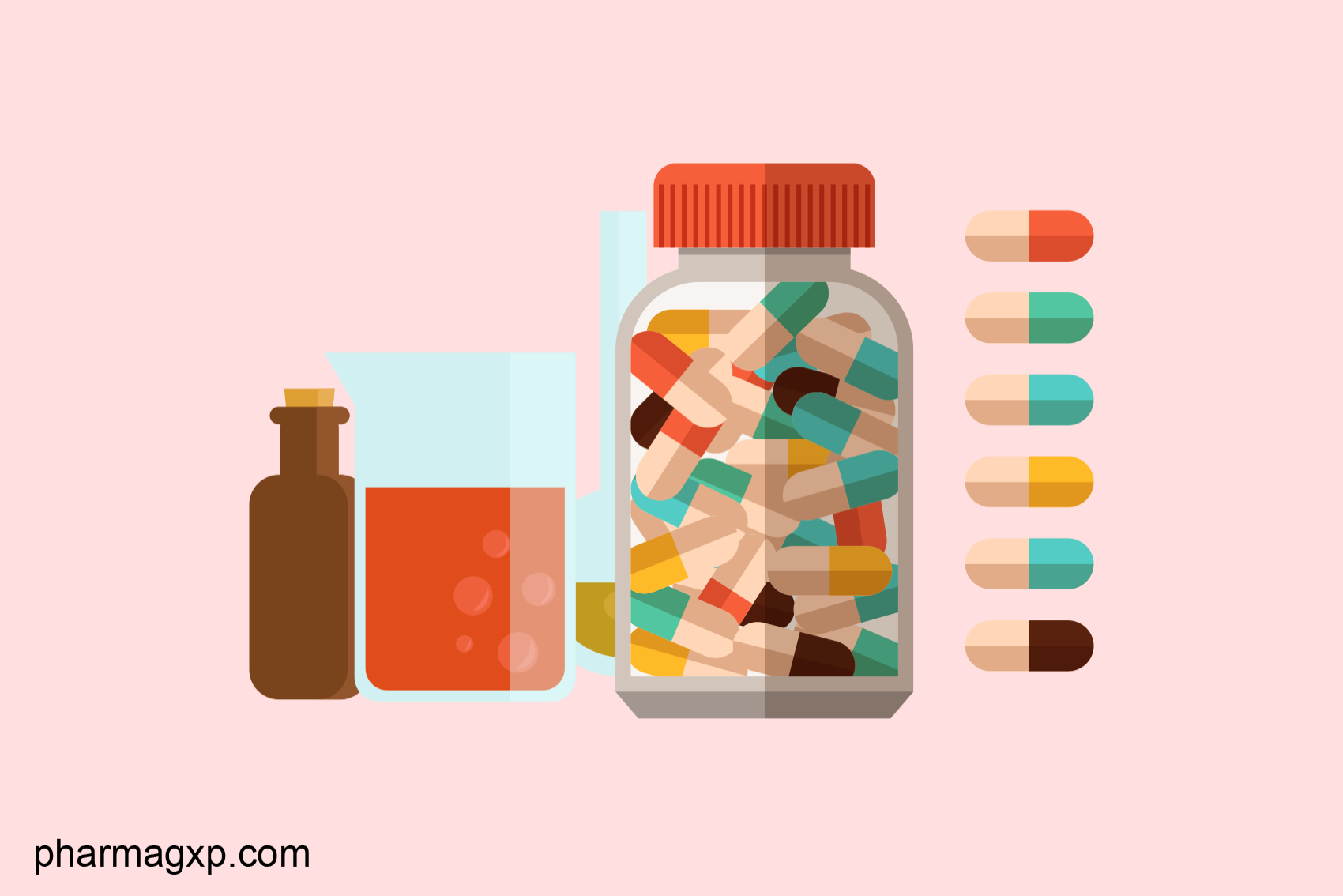
Only having in process checks or final testing doesn’t assure a quality product. “Quality” must be brought into the product through each step of manufacturing.
Drug manufacturing is a complex process, and each activity must be documented and verified to meet its purpose.
To ensure the safety, efficacy, and high-quality drugs or medical devices, Qualification and Validation activities are performed with the help of good documentation practices as part of the regulatory requirements.
In simple words, these activities ascertain whether the system is designed as needed and perform as intended.
Table of Content
Qualification
Qualification is objective evidence that equipment or system and its ancillary systems are correctly installed, work as expected, and fit for the intended use.
Crux of all definitions
Validation
Validation is the collection and assessment of data from process design to commercial phase, which establishes objective evidence that a process can consistently deliver a quality product.
Crux of all definitions
Difference between Qualification and Validation
Qualification is related to instruments and equipment. Meaning, instruments and equipment tend to qualify.
Validation is related to processes. Meaning, the processes tends to validate.
Pharmacopeil Forum, 2006:32(6), 1784-1794 USP General Chapter <1058>
Besides this, utilities, sometimes, also require validation based on risk assessment during the process development phase.
Critical utilities may include the electrical accessories, HVAC, Vacuum, WFI, Pure Steam, Purified Water, etc.
For utilities with controllable input-output, qualification may be sufficient and may not require validation.
Sometimes, equipment may require process validation instead of qualification if used for critical manufacturing steps. This makes sense as we challenge the equipment to show reproducible results for the critical operations.
Interpretation of these two terms slightly varies for medical devices compared to pharmaceuticals; however, the intent remains the same.
Medical devices follow ISO-13485 and 21 CFR Part 820 guidelines for these two approaches.
Here are the key differences between them.
Qualification | Validation |
---|---|
Is mainly for equipment and instruments. | Is mainly for: – Manufacturing process – Cleaning – Computer System – Software – Test Methods and sometimes for equipment used for critical process operations. |
Used to challenge the performance of equipment. | Used to challenge the performance of processes. |
Requirements include: URS, FDS, DQ, IQ, OQ, PQ, Calibration, Maintenance, etc. | Requirements include: 1. Process Design 2. Process Verification 3. Process Confirmation 4. Process Qualification Different types of Validation are: 1. Prospective Validation 2. Retrospective Validation 3. Concurrent Validation |
Does not demand a reproducible outcome. Only concerned about the proper functioning of the system and sub-systems. | Specifically intended to challenge reproducible outcomes. |
Ensures the equipment or system and its sub-systems are installed correctly, operate as required, and perform as intended. | Ensures the process is capable of producing consistent results within the approved specifications. |
Qualification is a part of Validation. | Validation is big umbrella under which Qualification is one vertical. |
To qualify the system, required documents are: URS, FDS, DQ, IQ, OQ, PQ, Calibration, Maintenance, etc. | For validation, required documents are: – SOPs – Qualification Status Report – Validation Master Plan – Validation Strategy – Validation Protocol – Validation Final Report |
Mostly, qualification of various equipment can be performed simultaneously. So, this can go in parallel. | Within validation, supporting processes require validation prior to validating the key process. And this goes in series. |
Re-qualification is needed for: 1. Significant modifications critical to the outcome 2. Post relocation 3. Software and control modifications 4. Periodic Schedule | Re-validation is needed for any changes in: 1. Process or its environment 2. Starting material 3. Packing material 4. Steps or Procedure 5. Equipment 6. Periodic Schedule |
Conclusion
Understanding the overall picture of their differences will surely help you effectively manage your efforts.
Qualification is part of the validation. V-model is the best way to interpret how the document life cycle revolves around distinct parts of validation.
Do you find it difficult to decide whether to qualify or validate your system? Either way, let me quickly know in the comment below.
Hi Saket
Is it a requirement documented that the calibration ranges used must meet or exceed process ranges. That you cannot use a linearity statement if the calibration range is inside the process range?
Either way, calibration requirements should meet the calibration outcomes.
Hello Saket,
Why the guidelines mention performance qualification for sterile only while non-sterile mentioned as process validation?
Thanks, Rasha for reaching out.
First thing first. Which guidelines you are talking about? Can you please provide reference? So that I can respond more meaningfully and actually could help you out.
Hello Saket,
Could you please help me with this?
Ring central is voip used for calls at our company. It’s used for calls over wifi including adverse events reporting. Should this be considered as infrastructure and qualified or validated as a system.
Hi Sudhakar, voice over IP is a communication tool and comes as a Category 1 I guess.
According to ISPE data integrity experts, since GAMP 5 category 1 software does not store or create data, it can be managed using good IT practices and routine assessments. As a result, category 1 solutions don’t need validation, only qualification. This does not mean that life sciences companies should not take steps to ensure the security of their software and infrastructure.